The Good Inside a Soapbox
There are some things even soap, no matter how good, can’t clean. We aren’t talking about what comes out of your mouth when you stub your toe.
Maybe you knew that Method became one of the fastest growing private companies in the country by taking on what’s inside the bottle and turning it green with naturally derived plant-based ingredients—formulas that keep in mind puppies and small humans who might put their mouths on things that mouths are not supposed to be put on—and making the outside something you might actually want to put on the counter, all while using recycled bottles to do it. Now the place where their products are made is doing its part, too. Method’s factory in the historic Pullman District of Chicago—dubbed “The South Side Soapbox”—is the first-ever LEED Platinum Certified manufacturing plant in its industry. But the commitment to leaving the world a better place goes deeper than badges on buildings.
How is a Cherry Tree a Model for a Building?
It’s worth noting William McDonough + Partners worked with Method on the design of the Soapbox. If you recognize McDonough’s name, it’s likely you read Cradle to Cradle, his book about not treating the earth like a drive-thru window. His model of how a manufacturing process could work came from the example of the cherry tree.

William McDonough’s sketch of a traditional factory and the Method factory. Courtesy William McDonough + Partners.
The purpose of the tree is to grow the tree, but it’s not the most perfectly efficient system ever—there are a lot of byproducts. The cherry tree expires gas—oxygen, but that makes it much easier to breathe. It produces much more fruit than it would ever need to provide a seed to replace itself, but these cherries are food for birds and bugs and all manner of microorganism. Its leaves wither and fall—but rather than merely collecting as forest fire fuel, these nourish the soil. Eventually, this soil supports a new cherry tree.
The lesson of the cherry tree is that in nature there is no such thing as waste. There are just valuable resources sometimes in the wrong place.
By the Numbers
- 230-foot-tall, 600kW turbine provides 30 percent of the annual energy consumption and a tall place for Method to declare it hearts Chicago.
- Three 35×35-foot solar-tracking panels follow the sun from sunrise to sunset to collect maximum wattage.
- Production, filling and distribution all happen under this 150,000-square-foot roof, which means the soap is driven 1,000 feet in a colorful forklift instead of 1,000 miles in a nitro-burning funny car (or tractor trailer equivalent) when it’s ready to be bottled and shipped.
- Bright, open and airy building with loads of natural sunlight helps employees actually enjoy their environment—a pretty novel concept in manufacturing plants (which usually do not have quite so many, if any, actual plants).
- In case anyone gets hungry while making soap, there’s 75,000 square feet of greenhouse on the roof run by Gotham Greens, producing about 500 tons of fresh vegetables (which goes to community markets and restaurants).
- An additional 1,500 square feet of roof supports a green canopy growing outside, which helps use less energy, improve air quality and reduce stormwater runoff.
- The facility uses low-flow fixtures and water recycling on the manufacturing line, but the majority of water used ends up in the product, so Method has partnered with The Nature Conservancy to recharge the aquifer, to the tune of 6 million gallons annually.
- The Soapbox ain’t the first factory on this dirt. Portions of the 22 acres had been designated an EPA Brownfield site, where heavy metals were removed from the soil before construction began. Method is using 2.5 acres of the site for manufacturing, restoring the remaining acreage to native prairie and open space where wildflowers and perennials now bloom.
- You can’t see it here but the Soapbox is near railroads, meaning product can be shipped by rail, which is much less fossil-fuel-burny than fleets of trucks.
- Since it opened in 2015, the Soapbox has reduced Method’s carbon emissions by 200-metric tons.
A conversation with Saskia van Gendt, Senior Director of Sustainability at Method and one of the People Against Dirty’s “Greenskeepers.”
What features, if any, were planned that didn’t make the final building and why?
Saskia van Gendt: From the beginning, we knew that we wanted to do something with the factory roof. Our sister brand Ecover pioneered green manufacturing with a beautiful undulating green roof on its factory, and we wanted to reference that in some way. One of the ideas we were tossing around was creating a rooftop butterfly garden. But pretty quickly we were introduced to Gotham Greens, a pioneer in urban agriculture, and we loved the idea of using the roof as a functional greenhouse that would be productive and benefit the Chicago community.
What changes or improvements have been made since it started operation?
SVG: We continue to increase our production capacity at the factory, adding new equipment and filling lines. Alongside that growth, we’ve been able to expand our commitment to hiring more people from the local community, training and developing skills for people without previous manufacturing experience. Some people who we hired, in the beginning, have been promoted to team leaders or into specializations within the factory.
Over time we’re also seeing the land around the factory–we own 22 acres but only 2.5 acres are developed—slowly transition into a native Illinois prairie.
From an environmental standpoint, we’re also always trying to optimize how we use water and energy—dialing in our wind turbine to produce more energy and identifying ways to reduce our processing water. Any energy needs that we aren’t producing onsite from our wind turbine and solar panels, we’re able to cover with wind energy through our utility. Over time we’re also seeing the land around the factory–we own 22 acres but only 2.5 acres are developed—slowly transition into a native Illinois prairie; 3 years ago we seeded native plants and constructed bioswales to capture water. Now we’re beginning to see a progression in the land with wildflowers and perennials taking hold, a beautiful contrast to the formerly polluted site it was a few years ago.
In what significant ways did the location influence the decision to base the factory in Chicago?
SVG: Location was the #1 influence for us landing in Chicago – and Pullman specifically. We knew we wanted to build in a city to respond to urban migration and provide jobs where people live. Since we use water in our products, we had to locate in a healthy watershed even though our roots point back to California. If we had to build a new building, it had to be on a formerly developed property, preferably a Brownfield. And we wanted proximity to the rail so that when we achieve scale, we can ship with a lower carbon footprint. Using these filters, we narrowed down from more than 100 locations to 3 sites in the Midwest. Ultimately the potential to provide jobs and improve the livelihoods of people on the south side of Chicago was the reason we made Pullman our home.
We want to be a part of a movement of green manufacturers creating a new economic potential for workers that includes skill development, growth opportunities and a fun and caring culture…and maybe an annual company-wide ping-pong tournament.
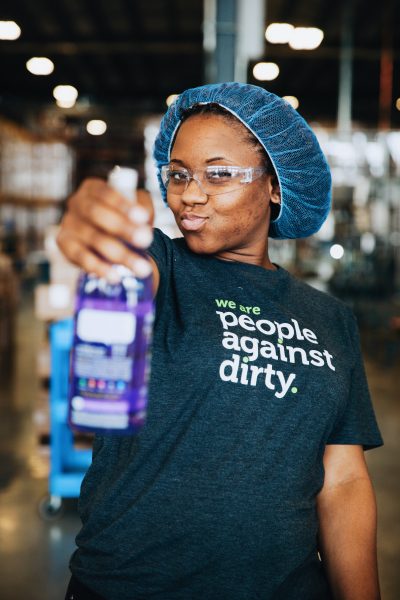
The People Against Dirty
What is the approach of Method and The Nature Conservancy’s water recharging partnership?
SVG: The Nature Conservancy provides technical assistance and support to farmers, helping them implement targeted water conservation practices. Using tested practices like no-till planting, drainage management or creating small scale wetlands, farmers can prevent evaporation and allow water to replenish the water table. TNC is also collaborating with Michigan State University to develop a calculator that quantifies the benefits of these practices, enabling more farmers and companies to replicate practices that will recharge the most water.
In general, what else can you tell us about the key features of the facility that we highlight the connection to Cradle to Cradle principles?
SVG: The Soapbox’s architect of record was William McDonough, the green building architect and co-author of Cradle to Cradle. His design and LEED construction integrated Cradle to Cradle principles from the beginning. We used majority recycled content materials and diverted construction materials for recycling. We rehabilitated the contaminated soil to make it a viable manufacturing site and now a native prairie ecosystem. Our processes use renewable energy from the sun and wind. And since all of our ingredients are selected with Cradle to Cradle certification in mind, all of the ingredients that we are using in the factory have been screened for human health and environmental criteria.
How can the Soapbox serve as a model for the future of manufacturing?
SVG: We hope we can demonstrate that you can benefit people and the planet while meeting operational and financial goals. The Soapbox is designed to be a great place to work with natural light and healthy conditions, and to be flexible and adaptive as our production demands change. Our integrated manufacturing with our bottle manufacturer, filling operation, decoration and warehousing under one roof is a model for eliminating carbon—we shortened the distance a bottle travels during production from 1,000 miles to 1,000 feet—while allowing us to operate more quickly and with flexibility. And we want to be a part of a movement of green manufacturers creating a new economic potential for workers that includes skill development, growth opportunities and a fun and caring culture…and maybe an annual company-wide ping-pong tournament.